Renault-Werk Batilly ist bereit für den nächsten Rekord
MONTAGEWERK Die vierte Generation des Renault Master steht vor der Tür. Für den von Grund auf neu entwickelten grossen Transporter hat die Renault Group auch die Prozesse im Montagewerk in Batilly (F) modernisiert.
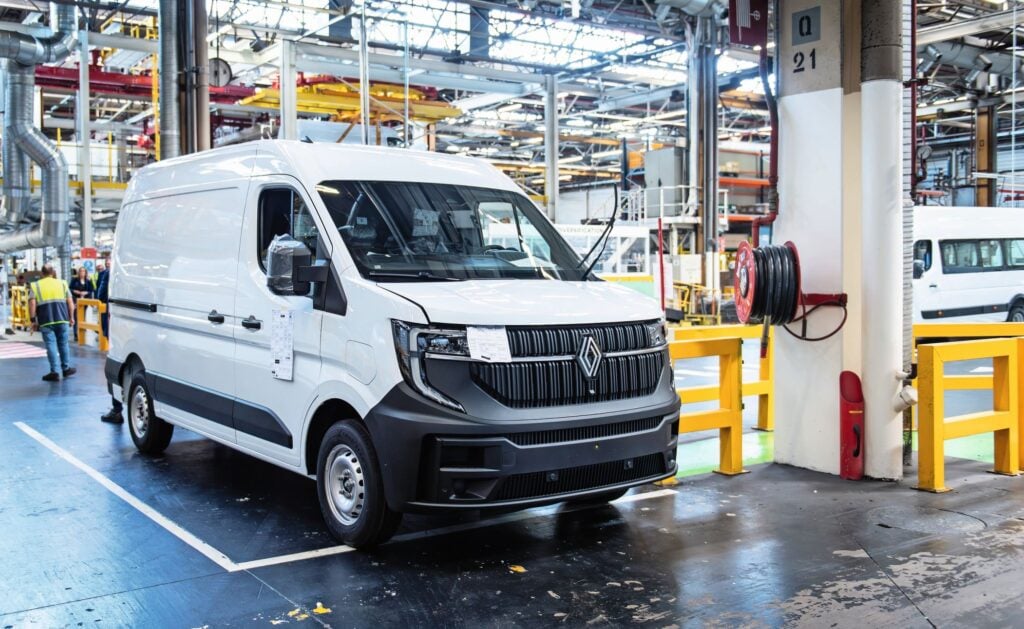
Noch letztes Jahr verzeichnete das Werk mit 150 261 produzierten Fahrzeugen einen Produktionsrekord und löste damit die bisherige Höchstmarke von 2019 ab. Das ab 1977 gebaute und seit 1980 in Betrieb stehende Werk Batilly beschäftigt heute 3100 Mitarbeitende und ist der grösste private Arbeitgeber des Départements. Seit 1999 im Drei-Schicht-Betrieb, verlassen täglich 720 Renault Master die Produktionslinien. Gebaut werden hier Master, Master Red Edition für das Renault-Trucks-Netzwerk, sowie der baugleiche Nissan Interstar. Es ist das einzige Werk für grosse Transporter in ganz Frankreich.
Alle Teile in Batilly angeliefert
Die Montage beginnt mit dem Karosseriebau. Komponenten und Teile wie Bleche, Motoren, Achsen etc. kommen aus anderen Renault-Fabriken oder von einem der 417 Zulieferer (davon 87 Prozent aus Frankreich). Der Teilekatalog umfasst 3903 Positionen. Nach dem Karosseriebau geht es zur Lackiererei, danach zur eigentlichen Montage, durch die Qualitätskontrolle und dann zur Auslieferung.
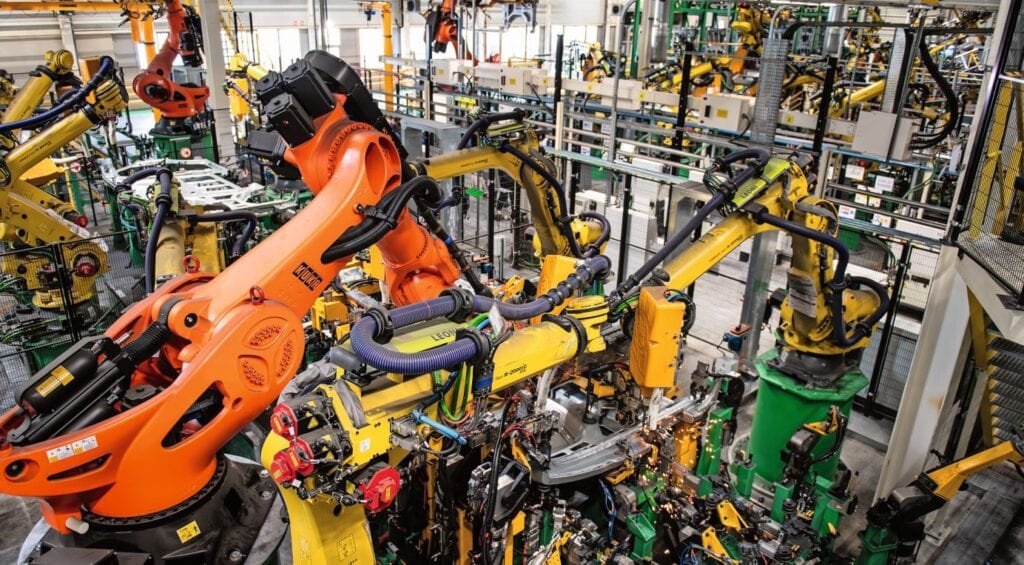
Im zu 95 Prozent automatisierten Karosseriebau («Body Shop») entsteht in vier Stunden die Rohkarosse der vierten Master-Generation in mehr als 40 möglichen Karosserieformen. 523 Roboter (davon 212 neue) setzen 6500 Schweisspunkte.
In der Lackiererei («Paint Shop») verbringt das Fahrzeug 10 Stunden. Dabei werden zwischen 5 und 20 kg Mastix (Dichtmasse) pro Fahrzeug aufgetragen. Zu den sieben bisherigen Serienlackierungen ist neu die Lancierungsfarbe Agave Blue hinzugekommen. Optional sind 300 weitere Rial-Farbtöne bestellbar.
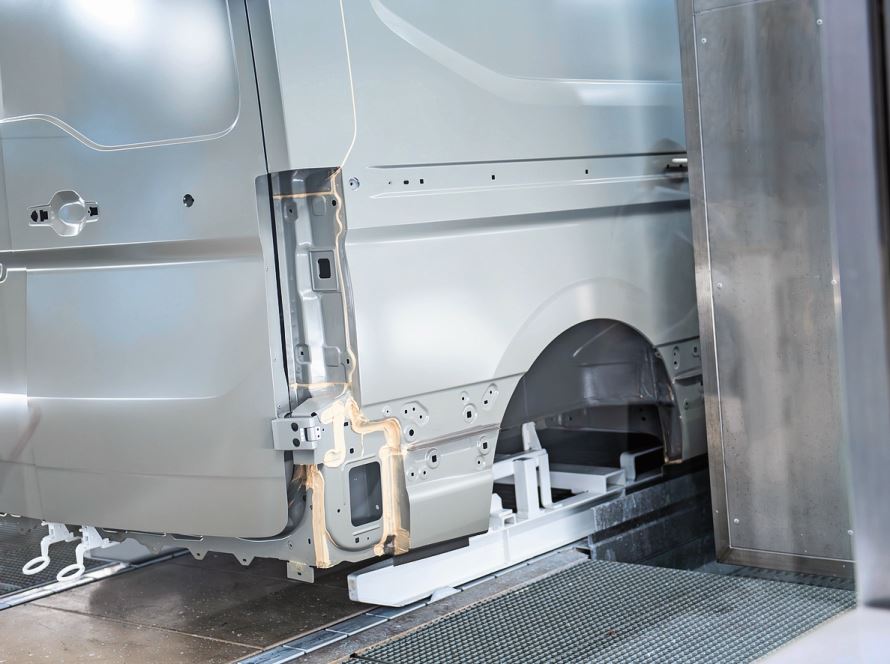
Die personalintensive Endmontage («Assembly»), wo Antriebsstrang, Elektrik, Licht, Cockpit und Interieur verbaut werden, dauert drei Stunden. Auf 1500 m² wurde eine neue Batteriemontage für die BEV-Versionen eingerichtet. Der Logistikbereich schliesslich wird täglich von 390 LKW angefahren, verfügt über zehn Lagerzonen und 105 Stapler.
Grössere Vielfalt auch beim Antrieb
Während bisher für die Anpassung der Produktion an eine neue Master-Generation die Fabrik für einige Wochen komplett still stand, erfolgte der Umbau diesmal parallel zum laufenden Betrieb. Bei unserem Besuch waren auf derselben Linie sowohl die neue vierte als auch die «alte» dritte Version des Renault Master zu sehen, wobei es sich bei Letzteren um die Abarbeitung der ausstehenden Bestellungen für den Export handelte. Die letzten Europaversionen waren bis Ende Juni fertiggestellt und ausgeliefert worden, da seit Juli in den europäischen Märkten verschärfte ADAS-Vorschriften (Sicherheits-Assistenten) gelten. Übrigens war per Ende Juni 2024 der Master mit 16,5 Prozent Marktanteil Nummer eins in Europa.
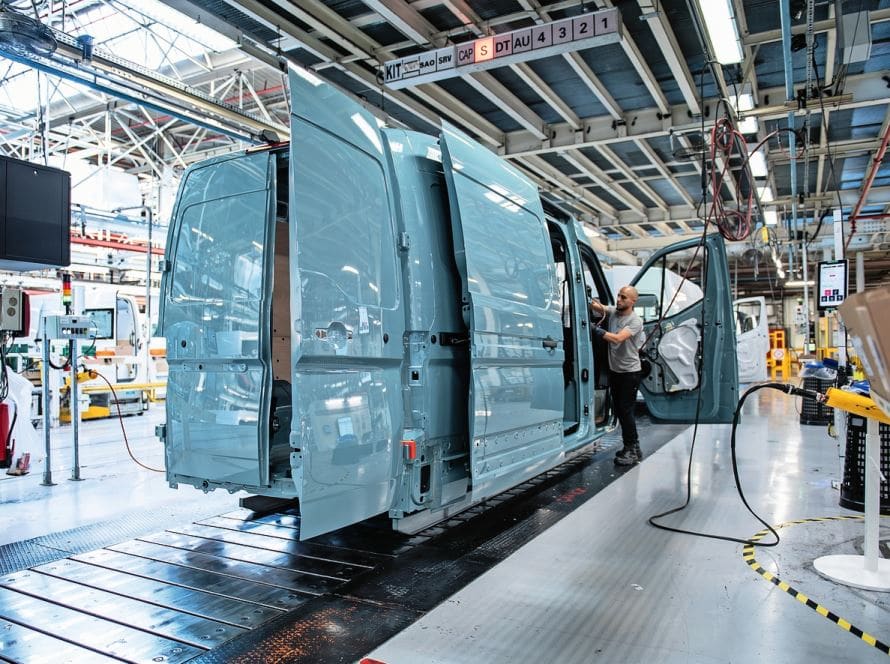
Nebst dem höheren Automatisierungsgrad wurden die Produktionslinien auch darauf vorbereitet, dass alle Antriebsvarianten («just in time» und «just in sequence») auf jeder Linie montiert werden können, was die Produktionskosten insbesondere für die batterieelektrischen Versionen (BEV) erheblich reduziert. Konkret sind das:
- Neue Blue DCI Dieselmotoren mit 105 bis 170 PS
- BEV mit 40- oder 87-kWh-Batterie (bis 460 km Reichweite)
- FCEV (H2-Brennstoffzelle) folgt zu einem späteren Zeitpunkt und wird ebenfalls im Werk Batilly gebaut
- Neue 9-Gang-Automatik und 20 ADAS (Fahrassistenten)
- Ebenfalls «inhouse» werden auch diverse Umbauten/Individualisierungen angeboten:
- Kofferaufbau, mit oder ohne Windabweiser auf dem Kabinendach und optionaler Hebebühne
- Rückfahrkamera mit Bildausgabe im mittleren Rückspiegel
- Rückwärts- und Dreiseitenkipper
- Polypropylen-Schutzplatten für Kastenwagen-Laderaum
- Verschliessbare Alukästen (etwa zwischen Pritsche und Kabine)
Hohe Umweltstandards in Batilly
Seit 1999 ist das Werk Batilly ISO 14001 Umwelt-zertifiziert. Es verfügt über 43 000 PV-Module, ein Recycling-Center und eine Wasserwiederaufbereitungsanlage. Der Stromverbrauch lag 2023 bei 71 299 MWh, das entspricht dem Verbrauch von 2400 Einfamilienhäusern (EFH). Gleichzeitig wurden 144 856 MWh Gas verbrannt (Heizbedarf von 3200 EFH). Die Produktion benötigte zudem 315 555 m³ Wasser (Bedarf von 6800 Einwohnern).
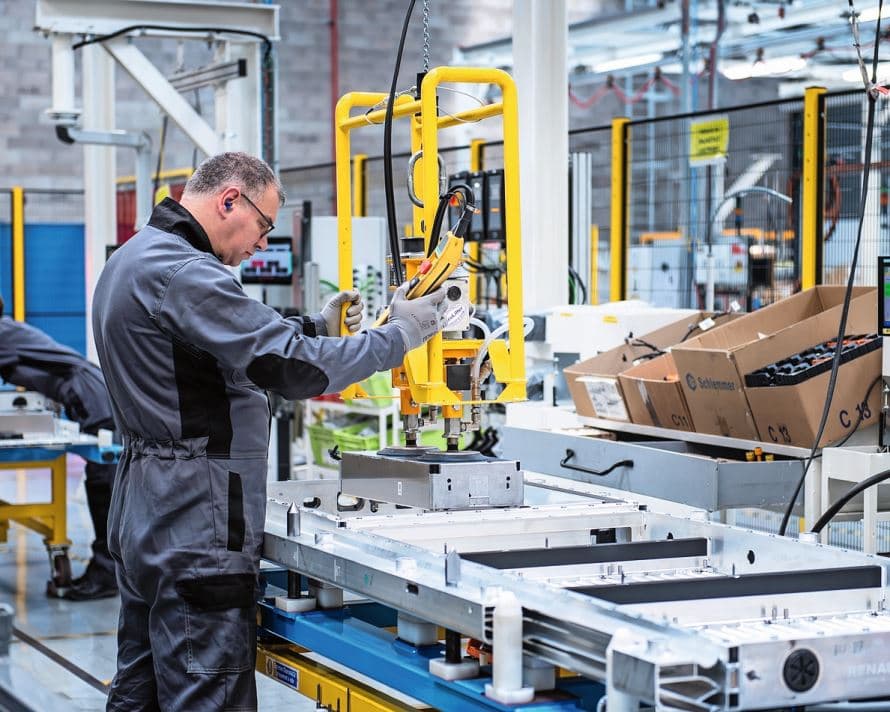
Das Werk und der Produktionsprozess sind digital durchgehend vernetzt. In verschiedenen Kontrollzentren, aber auch auf grossen Bildschirmen, stehen den Gruppenleitern und Mitarbeitenden transparent aktuelle Informationen und Kennzahlen zur Verfügung.
Dazu erhielten Mitarbeitende gesamthaft 110 000 Trainingsstunden, weitere Unterstützung gab es für die Spezialisierung für den Umgang mit Batterien, Robotern und Daten. Und schliesslich wurden neue 4.0-Skills erarbeitet, um bei Cybersicherheit, Künstlicher Intelligenz und Dekarbonisierung auf dem aktuellen Stand zu sein.